APROE has grown to become the premier facility setup partner for large companies to expand their product design and testing divisions. We work alongside architects and facility engineers to define, plan, and implement the required machines and accessories to help your team develop and test products at a rate only achievable with an in-house facility.
These are the steps we go through during a typical project:
- Define Scope: Will the facility be for prototyping, production or research? What is the project’s size, budget and timing?
- Source Machines: Research and select new and used machines to achieve facility objectives while staying within budget.
- Layout: Design a functional facility in CAD with necessary utilities, proper machine placement, safety and buffer zones.
- Accessorize: Communicate with user groups to assist in selection and positioning of required tools and support items.
- Take Facility Live: Install and test machines; on-site coordination of riggers, electricians, plumbers and other contractors.
- Customize: Create innovative tooling and fixtures, designed and manufactured by our in-house prototyping team.
- Education: Develop training curricula to guide staff on safe/proper machine use.
Prototyping and Research Facility Setup Process
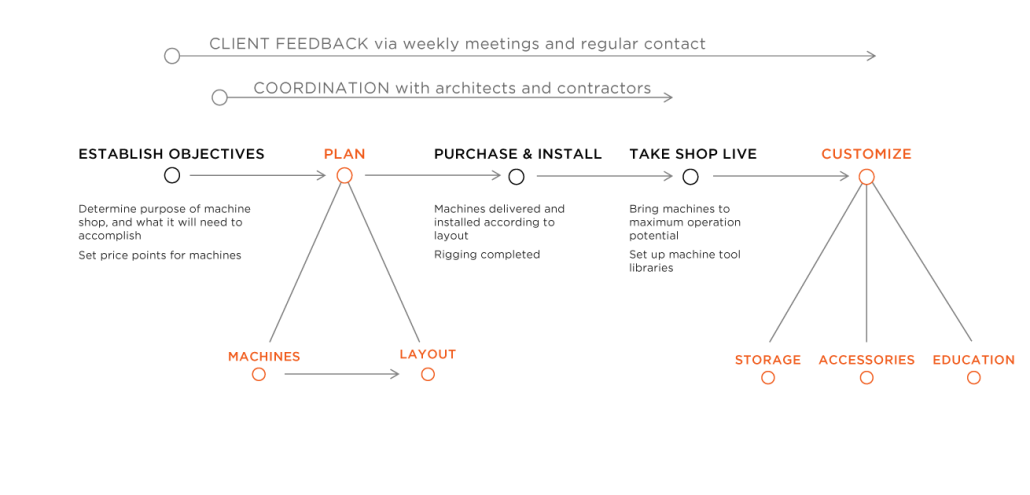
Finalize machine selection
Create 3D model of space and machines
Complete machine specifications
- Air
- Power
- Etc
Use 3D models and paper footprints to deliver optimal, efficient shop, per client’s goals
Architects begin permitting process once layout is established
Specify final machine tooling and accessories
Spec, order, fabricate and install storage options:
• Hand tools, including foam cutouts in tool drawers
• Cutting tools and bits
• Materials
• Hardware
Design and fabricate custom shop accessories:
• Welding fixtures
• Machine shielding
APROE creates custom classes, taught at your facility, to satisfy specific needs of various stakeholders:
• Risk Management/EHS
• Shop Managers
• Machine users